Building Green - Sustainable Sourcing in Cement and Steel Industries
Published on 03 Jun, 2024
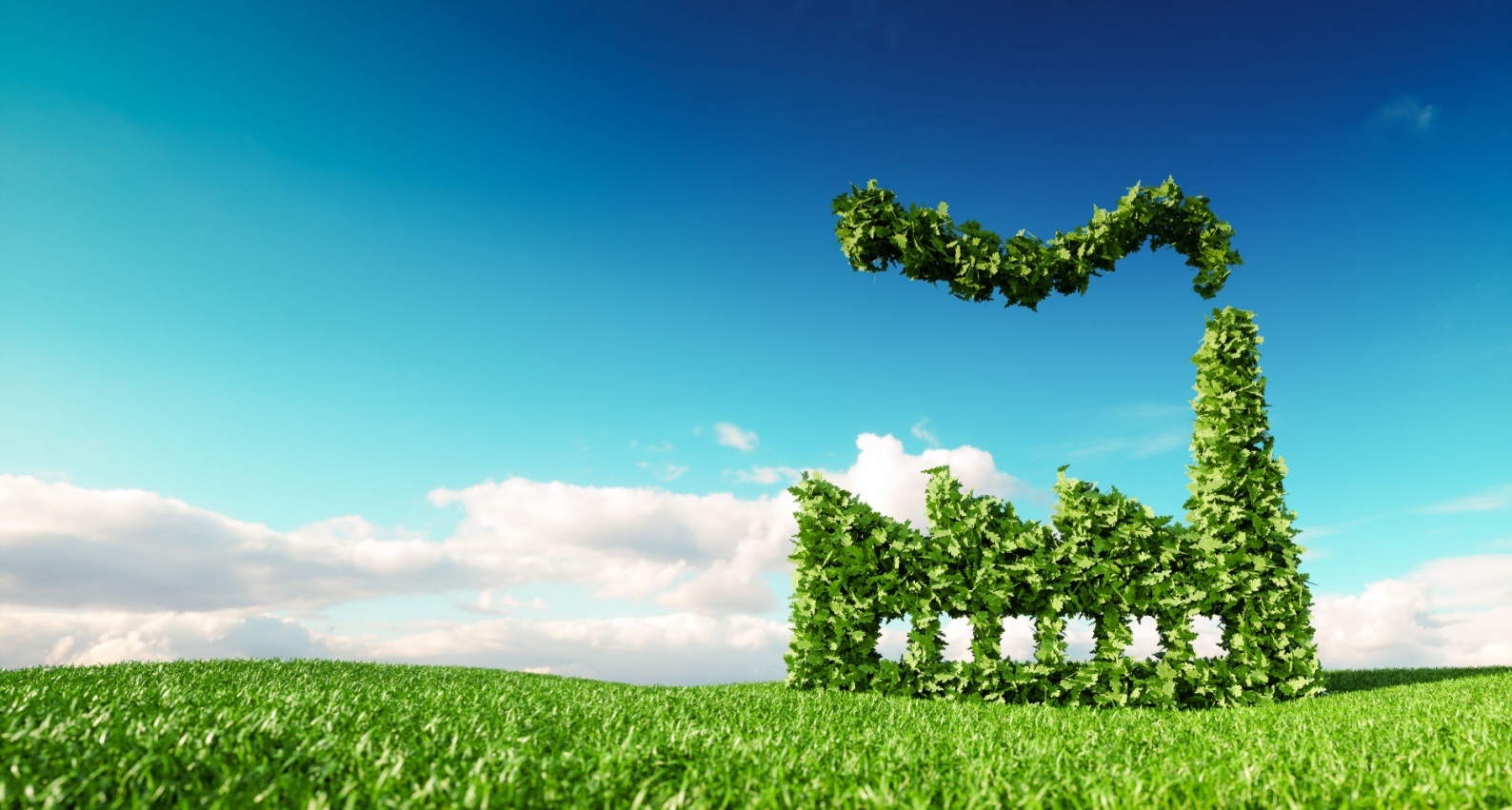
The transition towards sustainability in cement and steel industries is gaining momentum due to stricter environmental regulations and increasing consumer demand. Companies are embracing innovative strategies such as green procurement, alternative material sourcing, and renewable energy integration to reduce carbon emissions. However, several challenges persist, such as the inherent chemical processes and financial barriers that challenge the adoption of low-carbon technologies. Despite such challenges, initiatives like IDDI's Green Public Procurement Pledge and SteelZero drive industry-wide changes. Standardized emission benchmarks are essential for collaboration and to maximize impact.
Manufacturing companies increasingly prioritize decarbonization in their practices and in the sourcing of raw materials for several reasons: stricter environmental laws, growing demand from consumers and investors, and achieving cost efficiencies through optimization of energy consumption, among others. While decarbonization efforts in the transportation and power sectors have gained momentum, significant hurdles impede similar progress in cement and steel production, making it a critical but lagging area for achieving climate safety goals.
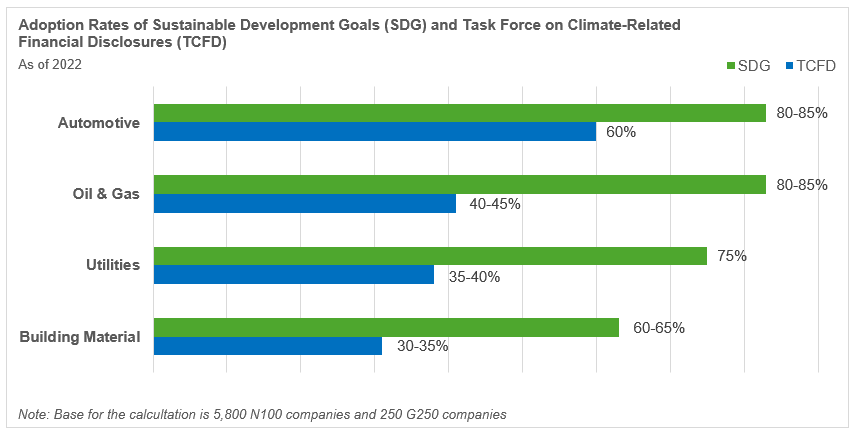
Over the past 4-5 years, cement and steel industries everywhere have evolved significantly in terms of implementing various measures to reduce their environmental footprint. Green purchasing is a powerful policy tool to stimulate early demand for low-carbon cement, concrete, and steel. This, combined with supportive policies, can significantly accelerate progress towards net-zero emissions in these industries.
There are four primary areas of focus in the cement and steel industries.
1. Sustainable Material Sourcing
The cement sector is progressively moving towards adopting alternative materials (ARMs) in lieu of clinker, the primary source of carbon dioxide (CO2) emissions in cement production. ARMs, such as electric arc furnace (EAF) slag, blast furnace slag, fly ash, natural pozzolans, and calcined clay, offer significant potential to reduce CO2 emissions associated with cement production.
The steel industry is also not far behind and has multiple green-material procurement initiatives such as sustainable sourcing of raw materials from suppliers who adhere to responsible mining practices, prioritization of worker safety, and minimizing of environmental degradation; increasing the use of recycled material in steel production reduces the demand for virgin raw material and consequently minimizes waste.
2. Renewable Energy Integration
Cement and steel plants have integrated renewable energy (RE) sources such as biomass, solar, and wind to power operations. This setup includes installing solar panels on site, investing in wind farms, or utilizing biomass boilers to generate heat. Also, cement and steel production involves high-temperature processes that give off significant amounts of waste heat. The industries have integrated waste-heat-recovery systems that capture the waste heat and convert it into electricity or utilize it for other industrial processes, thus reducing the need for fossil fuel.
3. Green Process / Technology Adoption
There is increasing emphasis on incorporating carbon capture, utilisation and storage (CCUS) technology into cement and concrete manufacturing. Captured CO2 can be utilized in several ways within the cement industry. It can be used in concrete production through carbonation processes, where CO2 is mineralized into carbonate minerals, effectively sequestering the carbon and improving the properties of concrete.
The steel industry has replaced blast furnace/basic oxygen furnace setups with EAF technology. EAFs are regarded as more ecologically sound than conventional blast furnaces due to their considerably reduced emission of greenhouse gases (GHGs) and pollutants like nitrous oxide (NOx) and sulfur oxide (SOx). With tightening environmental regulations worldwide, steel manufacturers are increasingly opting for EAFs to meet emission standard goals and to lessen their environmental impact.
4. Regulatory Push for Green Procurement
Several regional governments have adopted standards and policies for green procurement, aiming to promote sustainable practices and reduce the environmental impact of purchasing activities.
IDDI's Green Public Procurement (GPP) Pledge, initiated by the United Nations Industrial Development Organization in 2022, targets Canada, Germany, the UK, and the US. The program aims for 30% green procurement by 2025 and 100% by 2050. ConcreteZero, launched in the same year by WorldGBC and the World Business Council for Sustainable Development (WBCSD), operates globally and aims for 30% low-carbon procurement by 2025, 50% by 2030, and net zero emission procurement by 2050. The Federal Buy Clean Initiative, introduced by the General Services Administration (GSA) in 2021 in the US, sets a goal of 100% green procurement by 2050. The First Movers' Coalition (FMC), initiated by the World Economic Forum in 2021 and operational across the UK, India, Canada, Germany, Japan, the UAE, Saudi Arabia, Sweden, the US, and Brazil, aims for a 10% green procurement share by 2030. SteelZero, launched by ResponsibleSteel in 2020 on a global scale, targets 50% low-emission procurement by 2030 and net zero emission procurement by 2050.
These initiatives collectively strive to accelerate the transition to a more sustainable economy by setting ambitious targets for green procurement across various regions.
Challenges in the Market
Decarbonizing steel and cement production poses unique challenges compared with other industries. Some of the several reasons are listed here.
- Inherent chemical processes: CO2 emissions are a natural byproduct of chemical reactions integral to steel and cement manufacturing.
- Established practices and aging infrastructure: The industry’s reliance on long-standing production methods and the gradual replacement of outdated equipment hinder the pace of adaptation of sustainable practices.
- Financial barriers to low-carbon alternative technologies: The initial investment required for the adoption of low-carbon technologies (e.g., CCUS, alternative fuel, EAF) surpasses that needed for conventional methods.
Conclusion
Green procurement is transforming the cement and steel industries, pushing for sustainable practices across the value chain. Suppliers and producers face growing pressure to adopt eco-friendly methods like sustainable sourcing, lower-emission production, and recycled material use. Governments and businesses prioritizing low-carbon options drive innovation and investment in these areas. This shift will significantly enhance industry sustainability, contributing to a greener economy.
Governments can leverage their buying power to promote low-carbon materials to accelerate industrial decarbonization. Standardized emissions benchmarks are crucial. This ensures consistent measurement across initiatives, streamlining collaboration and maximizing environmental impact.