Global Semiconductor Chip Shortage – Extending to 2022
Published on 06 Jan, 2022
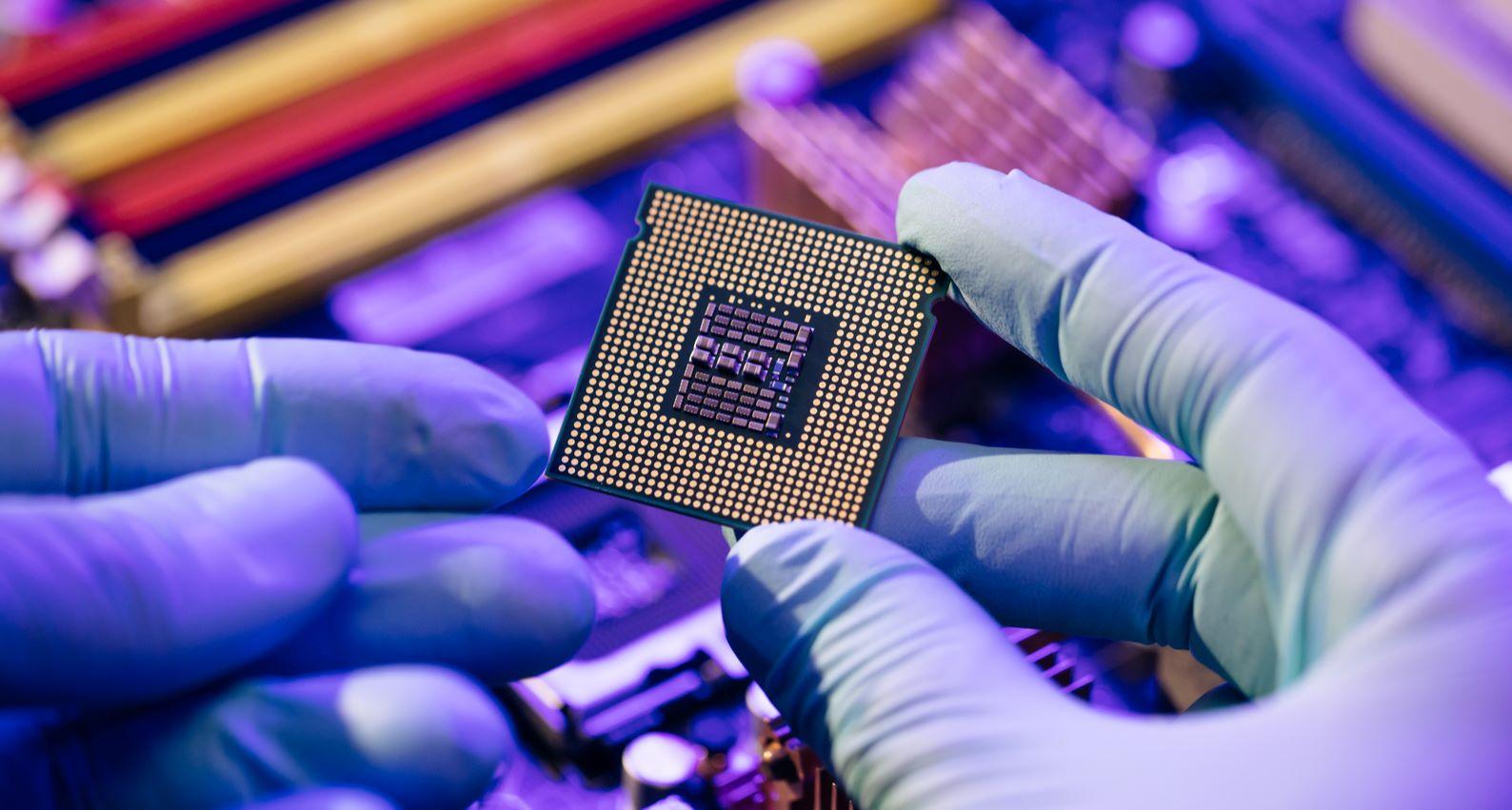
Semiconductors are the foundation of everything digital in today’s world – from transportation and AI to 5G, quantum computing, and beyond. The worldwide shortage of semiconductors that began in late 2020 emphasized the criticality of these specialized components. Although the industry faced severe supply challenges before the pandemic, the restrictions and lockdown imposed across the globe fueled the shortage. This situation has affected the automotive industry and electronics market the most. Some of the world’s leading auto manufacturers and technology companies are developing strategies to resolve this issue, while semiconductor manufacturers across the globe aim to ramp up production to meet the exceeding demand.
Introduction
With technology advancement across several sectors, semiconductors are literally the “heart” of billions of products, ranging from smartphones, computers, data centers, household appliances, laptops, tablets, smart devices, vehicles, life-saving pharmaceutical devices, ATMs, agri-tech equipment, and more. We are now in a world where every industry is either enabled by or dependent on semiconductors. Digitization drives the continued need for more chips, assisted by the four superpowers of AI, ubiquitous computing, cloud-to-edge infrastructure, and pervasive connectivity.
Figure 1 – Everyday products that rely on microchips
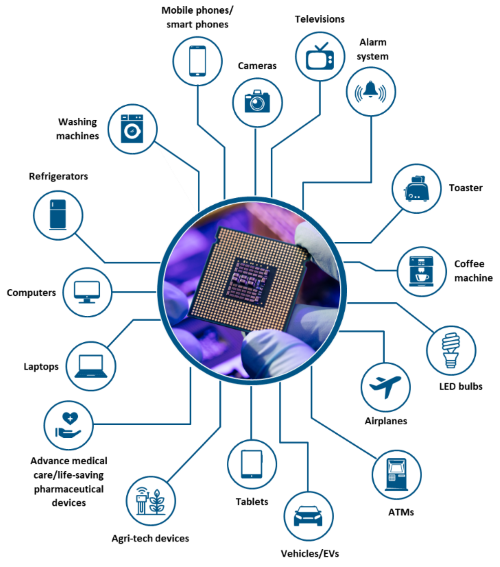
Case study – Auto Industry
Semiconductors are important components in the manufacture of automobiles and mainly used for power management, vehicle control, sensing, displays, and safety features. The acute shortage of semiconductor chips negatively affected global vehicle production in 2021 and is likely to extend to 2022, leading to huge losses for the auto industry. The global auto industry may produce 9.4 million to 11 million fewer vehicles in 2021 due to this shortage. As a result of the ongoing supply disruption, several vehicle manufacturers are likely to face difficulties until the second half of 2022. The chip shortage has negatively impacted vehicle delivery, leading to delays across the supply chain. In addition to delays in vehicle delivery, global carmakers have started discarding some features and high-end electronic components temporarily to cope with the chip shortage.
Figure 2 – Global Integrated Circuit (IC) unit shipment across various downturns, quarterly, 1990 to Q2 2021 (log scale)
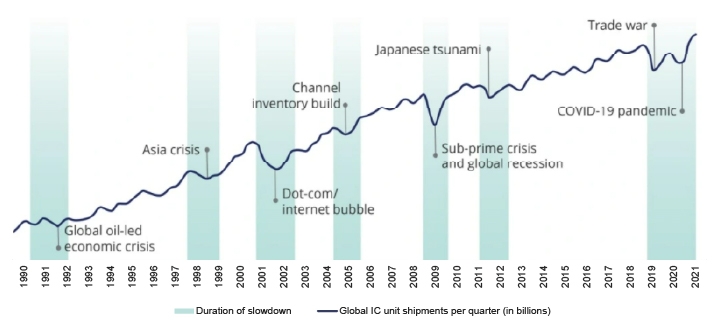
Source: Deloitte analysis based on secondary research and data gathered from publicly available articles and reports.
Causes
The demand for microchips exceeded supply even in the pre-pandemic era. The spread of COVID-19 globally created the perfect storm for the semiconductor industry, resulting in a severe supply crunch. First, as the global stay-at-home orders and lockdowns resulted in unprecedented usage of smartphones, laptops, and streaming devices, the already excessive demand for chips shot up. Second, the worldwide shutdown of production facilities halted chip production temporarily. Finally, massive supply chain bottlenecks were witnessed, as some major ports across the world ceased operations. The global chip crisis is a combination of various events, with the snowball effect of the pandemic being the primary reason, followed by the US–China trade war and drought in Taiwan. The semiconductor shortage was not caused by a single incident or event; rather, a series of events contributed to this situation.
Struggles during the COVID-19 crisis
Demand in the auto industry dropped substantially in the first half of 2020. Moreover, while new vehicle sales improved in the second half of 2020, the highly unclear sales outlook at the time meant that automakers did not meaningfully increase their semiconductor orders. At the same time, the shift to remote working and the associated greater need for connectivity significantly drove consumer demand for servers, PCs, laptops, and equipment for wired communications, all of which considerably depend on semiconductor chips. Even as the auto industry significantly reduced chip orders, other markets encountered an increased need.
Lack of new capacity
In recent years, the semiconductor industry has matured and achieved greater scale through consolidation. Although the capacity has expanded steadily, the industry witnessed an average annual growth of around 4% in line with sales. In the last decade, semiconductor utilization was constantly high at or above 80%. The utilization rate in 2020 reached around 90%, which many industry leaders regarded as full utilization, since exceeding that level often results in excessively long lead times. While the semiconductor industry increased its production capacity by nearly 180% since 2000, its total capacity remains nearly exhausted at the current high utilization rate.
Geopolitical tension
The global chip crisis and geopolitical tension with China have shifted the focus back to the semiconductor industry. The US wants to reinstate its leading position in chip manufacturing. Under the leadership of President Joe Biden, the US aims to reduce its dependency on chipmakers based in Asia by looking for ways to bring manufacturing back to the US. The industry has its eyes set on the increasing tension between China and Taiwan amid the global chip crisis.
As a result of geopolitical tension, some consumer-electronics manufacturers significantly increased their stock level of chips to sail through a period of limited access to chip manufacturing. McKinsey & Company reported that such stockpiling caused a rise in semiconductor demand of 5% to 10% in the wireless market, which is equivalent to one-third of the auto-market chip sales.
Contract terms
The standard contracts for procuring parts in the auto industry are significantly different from other industries, as they are more often governed by long-term binding agreements, also termed take-or-pay deals, and provide semiconductor manufacturers purchase orders beyond 6 to 12 months. Amid a highly complex and heavily outsourced auto supply chain, the chip-sourcing commitment cycle for the auto industry tends to be short term, especially for binding purchase commitments on the order of a few weeks to a few months. Semiconductor manufacturers are now dedicated to traditional, long-term contracts from other fast-acting industries, although the auto industry has had a good standing for steady demand in the past.
Limited stock
Just-in-time manufacturing practices are widely leveraged in the auto supply chain, as they can increase efficiency and minimize waste by maintaining low inventory levels. Companies may benefit financially because of reduced inventory levels in regular business conditions. However, in the event of an unexpected shortage, this practice may immediately disrupt the entire supply chain. Many players across industries had a highly limited stock of chips to survive the crisis, as most failed to predict the chip shortage.Just-in-time manufacturing practices are widely leveraged in the auto supply chain, as they can increase efficiency and minimize waste by maintaining low inventory levels. Companies may benefit financially because of reduced inventory levels in regular business conditions. However, in the event of an unexpected shortage, this practice may immediately disrupt the entire supply chain. Many players across industries had a highly limited stock of chips to survive the crisis, as most failed to predict the chip shortage.
5G rollout and overlapping chip demand
The demand for semiconductors differs by node size in the industry. The most advanced chips in small ranges are 14 and 7 nanometers or smaller. These are increasingly used in several leading-edge technology applications but not particularly required by automakers. An expansive rollout of 5G services warrants a huge number of radio-frequency semiconductor chips and large node sizes as auto chips. This also holds true for power-electronic chips needed to boot up PCs and servers. This amount of overlap implies that as the 5G rollout occurs over the next few years, auto manufacturers might face an ongoing shortage of chips.
Figure 3 – Surging Demand for EVs, 5G Smartphones and PCs is Driving Chip Demand
Annual shipment of devices including growth rates
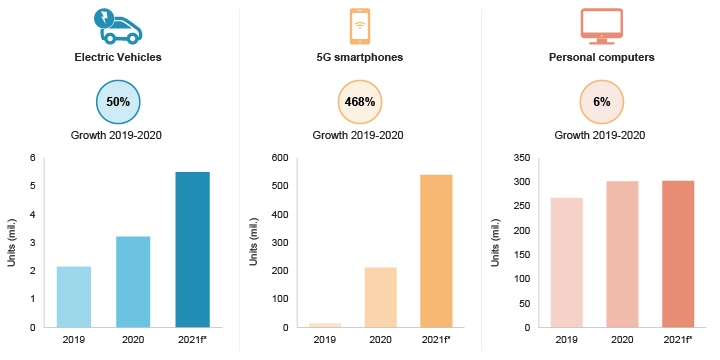
Source: S&P Global Ratings
Industries Impacted
More than 150 industries have been impacted by the chip shortage, but some have been hit much harder than others. The global semiconductor shortage has affected several industries for over a year now. Resultantly, industries are presented with two options: paying more for a product and getting it considerably faster or waiting a little more and getting products at the market rate. The shortage has affected the production of several household appliances, smartphones, laptops, printers, gaming consoles, PCs, automobiles, airplanes, and medical devices, among others.
Auto Industry
The auto industry accounts for around 10% of the global semiconductor sales. The chip shortage has severely impacted some of the biggest names in the industry, including Tesla, Ford, General Motors, and BMW. About 17 car manufacturers in North America and Europe have slowed or stopped production due to lack of chips. Amid the semiconductor supply shortage, the global auto industry is expected to witness a loss of $60.6 billion in revenue in 2021 and faces an estimated overall loss of $210 billion in revenue.
Consumer Electronics and Household Appliances
Similar to the auto industry, the global chip shortage will have a fundamental impact on the consumer electronics segment. The shortage of chips could not only lead to lower supply of electronic goods but also trigger an increase in prices. The demand for consumer electronics such as smartphones, laptops, and desktop PCs rose throughout the pandemic due to the switch to virtual learning among students and rise in remote working. While the global chip shortage is pushing up prices of laptops, printers, CPUs, and gaming consoles, production of top-selling devices, including smartphones and household appliances such as microwaves and refrigerators, also fall prey to the global chip shortage. HP is expected to increase the price of its printers by almost 20%. Sony has also hinted that it will not produce enough supplies of the PlayStation 5 console going forward in 2022.
Data Centers
During the pandemic, most chip fabrication companies such as Global Foundries, Samsung Foundries, and TSMC prioritized high-margin orders from PC and data center customers. While this has given data centers a competitive advantage, it is unfair to say that data centers have not been affected by the chip shortage. Data centers have struggled to source some components such as capacitors, BMC chips, circuit boards, and resistors, which are required to put together their data center switching systems. The chip shortage has led to several challenges for data centers, including reduced assembly capacity and extended lead times due to substrate and wafer shortage.
LED & Lighting Fixtures
The chip shortage also affected LED supply, and the demand for smart homes slightly declined as the pandemic slowed down or even stopped construction, remodeling, and improvement for residential and commercial properties.
Current Situation
The crisis appeared to ease during August 2021, but the situation is beginning to worsen. Smartphone manufacturers have been relatively protected thus far as they had existing stock of chips. However, the pressure is building on them and they too are starting to suffer. Gaming consoles, including the newly launched PlayStation 5 and Xbox Series X, have been in short supply. Foundries are increasing wafer prices, resulting in chip manufacturers raising device prices.
The global semiconductor demand remained high in October, with y-o-y sales increasing substantially across major regional markets. In November 2021, the Semiconductor Industry Association (SIA) reported global semiconductor sales of $144.8 billion for Q3 2021, an increase of 27.6% over that in Q3 2020 and 7.4% more than that in Q2 2021. With the industry aiming to ramp up chip production, the highest number of semiconductor units were shipped during Q3 2021, a milestone compared with that in any other quarter in the market’s history.
As the situation stands, the global chip crisis still persists. Prices of many electronic goods and components are expected to rise 1% to 3%. The global chip shortage has deteriorated in the last few months, with more than 8.2 million vehicles already taken out of production. The total reduction for the full year is estimated between 9.4 million to 11.0 million.
The chip shortage is disrupting auto businesses across the value chain as OEMs and their suppliers seek alternate ways to procure reliable chip sources. As semiconductor manufacturers struggle to keep up with the demand and auto players debate their next move, both the industries must align their short- and long-term strategies to withstand the supply-chain disruption. The demand surge and supply constraints causing the shortage are not one-off events. The fierce competition for chips and rising demand for electronics persist.
Companies such as Qualcomm and Apple design their own chips using the advanced ARM architecture software but outsource manufacturing to companies such as Taiwan Semiconductor Manufacturing Company (TSMC), the largest contract manufacturer for chips in the world. Recently, Intel outsourced some manufacturing to TSMC amid the chip shortage.
Prospects for recovery
It is highly unlikely that the global semiconductor shortage will resolve in the short term, mainly because of factors such as the increasingly sophisticated chips needed in auto design and complexity of semiconductor manufacturing. As a result, OEMs might have to consider some short- and long-term strategies as businesses deal with the imbalance in semiconductor supply and demand.
Short-term strategies
In light of the current situation, the supply and demand imbalance for semiconductors shows no sign of settling in the short term. This is because the normal lead times for semiconductor production can go beyond four months for products already well established in an assembly line.
Increasing capacity by moving a product to another manufacturing site in existing plants usually adds six months. Changing foundries or switching to a different manufacturer generally adds another year or more because the chip’s design requires modifications to match the specific manufacturing operations of the new partner.
As the situation stands for the auto industry, chip capacity will not match demand in the short term. This is mostly because of the sustained increase in volume and sophistication levels of chips required to develop new technologies, such as autonomous driving and advanced driver-assistance systems.
Some of the world’s leading companies have taken several measures to deal with the current situation. Many corporates have established dedicated war rooms that combine their supply and demand intelligence to create better transparency and develop strategies to tackle the issue. For example, automatically developed dashboards can combine data from multiple sources, such as a company’s supply chain and a semiconductor manufacturer’s commitments. The use of analytics to match demand and supply assists in overcoming the issue with an error-prone and cumbersome manual effort.
Several auto manufacturers and tier-one suppliers consistently collect and analyze highly sophisticated intelligence on chip-manufacturing locations and semiconductor value chain. Company leaders try to reassess the competitive landscape regularly by weighing the technological applications for prioritization at the level of the individual chips required to make informed decisions.
Solving long-term issues
In the long term, it is important for the auto industry to rethink a way to change the structure of contracts for sourcing semiconductors. In this regard, a good starting point would be for OEMs and tier-one players to make binding up-front volume commitments. A more stable risk-sharing strategy aligned with the value chain might help drive adoption rates.
Additionally, companies might have to reassess the current just-in-time delivery practices and low inventory levels across their value chains. Since many government leaders are now alarmed about the instability of supply chains and prospects of depending on a single supplier or distant countries for essential components, companies might need to align with government strategies that encourage regional sourcing.
Companies can also opt to invest in supply-chain resilience, with a clear view of their reliance on selected components and supply uncertainties. These investments might range from regulating pricing levels with supply assurances to bundling volumes and achieving greater control in the negotiation process to spending on dual-source manufacturing qualification in cooperation with semiconductor suppliers.
What Lies Ahead?
The chip shortage is expected to continue until 2023 due to strained supply lines and long lead times in the semiconductor industry. With technology advancements in several industries and roll-out of 5G services, the demand for PCs, smartphones, consumer electronics, laptops, and other smart devices is projected to remain high over the next few years. In such a situation, retailers may find it increasingly difficult to cater to the skyrocketing demand and consumers may have to face the ultimate burden. Chip shortage is expected to continue in Q2–Q3 of FY22 and supplies are expected to improve in a staggered manner.
It is crucial that semiconductor manufacturing and other companies that require chips for their products take immediate action to develop a more robust supply chain for years to come. These steps help mitigate risks, minimize disruption to business operations, lay the groundwork, and set the stage for short- and long-term strategies requiring significant investment in resources and time.
The pressure on capacity is likely to continue for some time. We will undoubtedly remain in a constrained environment given that the demand for semiconductors across the world is not slowing down. While the supply is expected to remain constrained, the demand is set to remain high, extending the shortage to last throughout 2022 and into 2023. IDC projects the semiconductor market to grow 17.3% in 2021 and reach potential overcapacity by 2023. Despite the current situation, the market is expected to reach $600 billion by 2025 and $1 trillion by the end of this decade.
Figure 4 – Global Semiconductor Capacity: Percentage share by region, 1990 – 2025
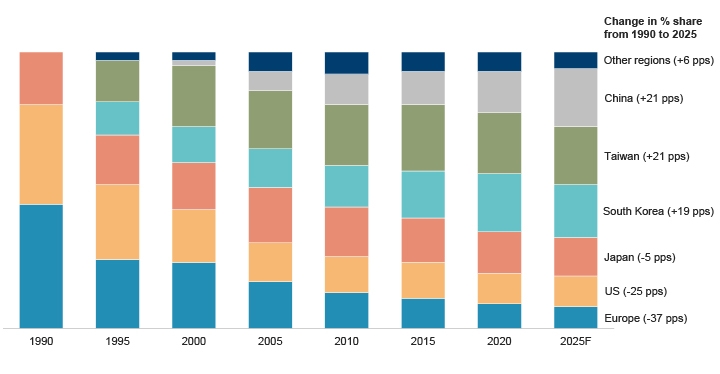
Source: Deloitte analysis based on information gathered from publicly available third party sources
Figure 5 – More than 85% chip foundry capacity is concentrated in the APAC region
Worldwide foundry capacity share by region, 2021 (projected)
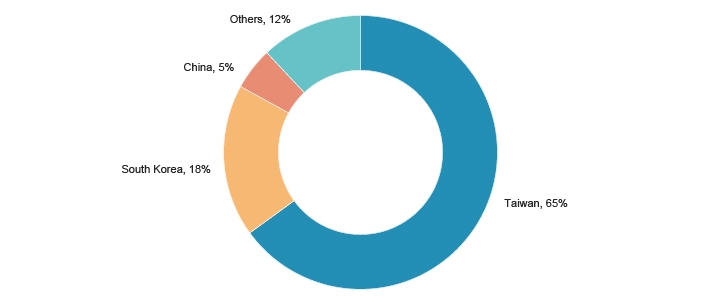
Note: Others mainly include Europe, North America and Japan Source: Deloitte
Conclusion
In conclusion, the semiconductor chip shortage is as real as it gets and an issue for various industries, which ultimately leads to a weak economy. Everyone, including regular consumers, are affected. In the last few months, most brands have hiked car prices, and the prices of smartphones, even the budget variants, are increasing. In addition, GPU prices are considerably up and it is a bad time to build PCs. In simple terms, the crisis is far from over and might spread to other industries. The situation could normalize by 2023, but the world is still trying to get around the issue and find solutions and substitutes wherever possible.