Carbon Capture – Moving Toward Net-Zero Emissions
Published on 24 Mar, 2023
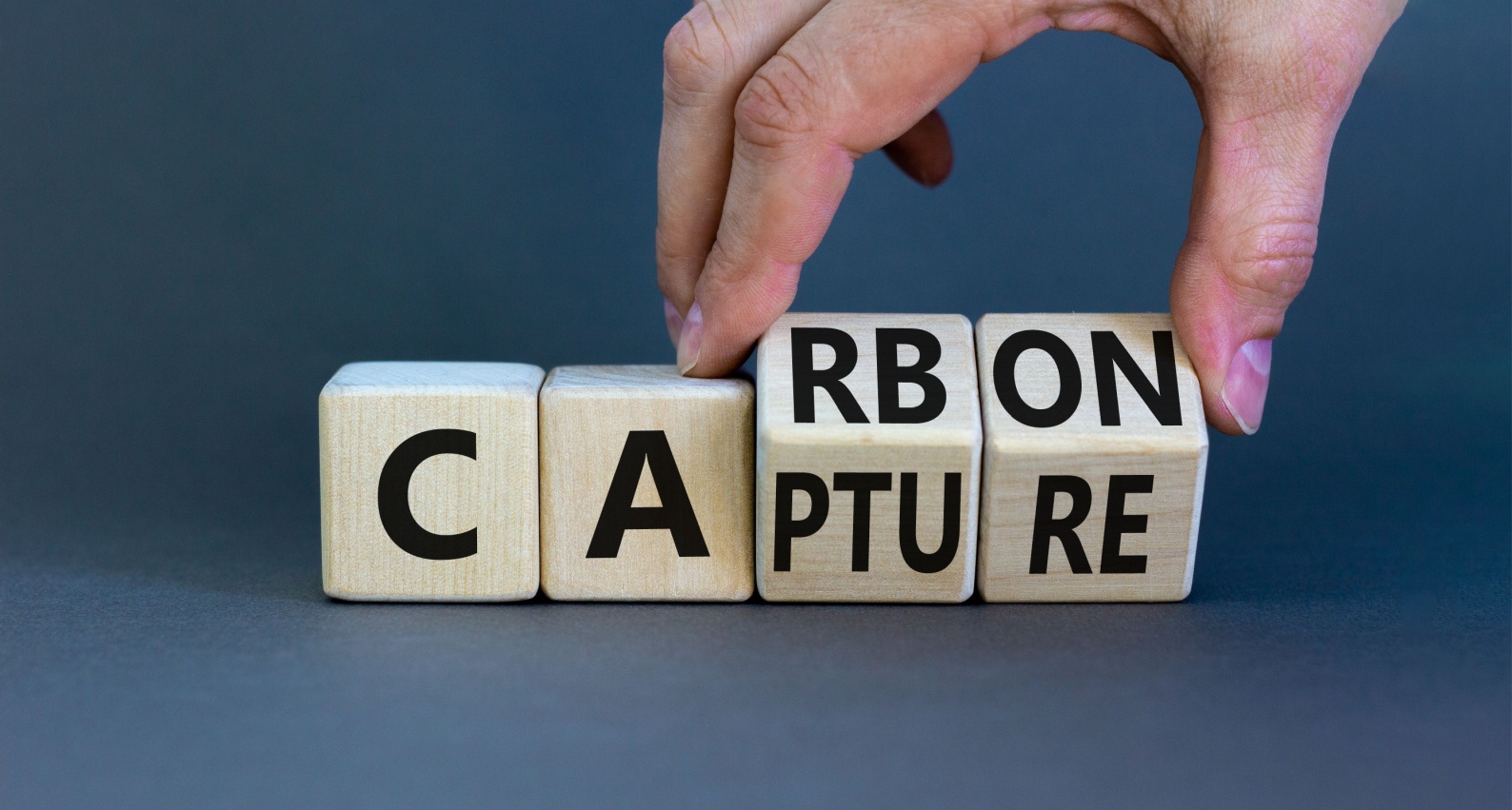
To save the planet from climate change, countries and organizations are working toward achieving net-zero emissions. Capture, utilization, and storage of carbon emerged as a leading strategy for limiting the global temperature rise. However, these technologies are expensive to implement in factories and manufacturing facilities. In addition, each technology comes with its set of limitations. If these obstacles can be surmounted, carbon capture can be widely implemented and contribute to a positive environmental impact.
Our planet is facing an existential crisis due to climate change. Carbon dioxide (CO2) emissions significantly damaged the atmosphere and are a major cause of global warming. Countries have united to tackle this crisis, and innovations and technologies to reduce carbon emissions are undergoing testing. To reduce the global temperature by 2°C by 2050, CO2 emissions must be reduced by 50% of the current levels.
Any industry that uses fossil fuels produces CO2. Power plants are the world’s largest carbon emitters. Additionally, the production of steel and cement generates massive CO2 emissions. Until now, most technologies focused on finding carbon capture utilization and storage (CCUS) solutions for power plants. However, companies and startups are refocusing their efforts on finding alternative methods to reduce emissions in other industries.
Carbon-Capture Strategies:
The CCUS field has essentially two types of carbon capture techniques, namely post-combustion and pre-combustion.
- Post-combustion carbon capture: Post-combustion carbon capture is the process of removing CO2 from the exhaust gases once the fuel is completely burned.

Following are some techniques for post-combustion capture:
- Solvent absorption
- Adsorption
- Membrane technology
- Cryogenic separation
Solvent absorption is the most prevalent technology used to separate CO2 from waste gas streams as it is cost-effective compared to other technologies in the domain. This method is applied in various industries, such as fuel production, ethylene oxide production, power plants, cement, and iron & steel manufacturing.
A sub-technique under post-combustion capture is oxy-fuel combustion. Oxy-fuel combustion is a carbon capture strategy in which the fuel is burned with nearly pure oxygen instead of air. The flue gas produced is high in CO2 and devoid of nitrogen and its components, such as nitrogen oxides (NOx). This eliminates the need for chemicals or other methods to separate CO2 from flue gas. However, oxygen is costly, and its production has significant negative environmental effects, including high CO2 emissions.
It can only be used in processes involving oxy-rich combustion, such as the production of cement, iron and steel, and electricity in fossil-fuel-powered plants.
- Pre-combustion carbon capture: The process of removing CO2 from the source before the completion of the combustion process is known as pre-combustion carbon capture.
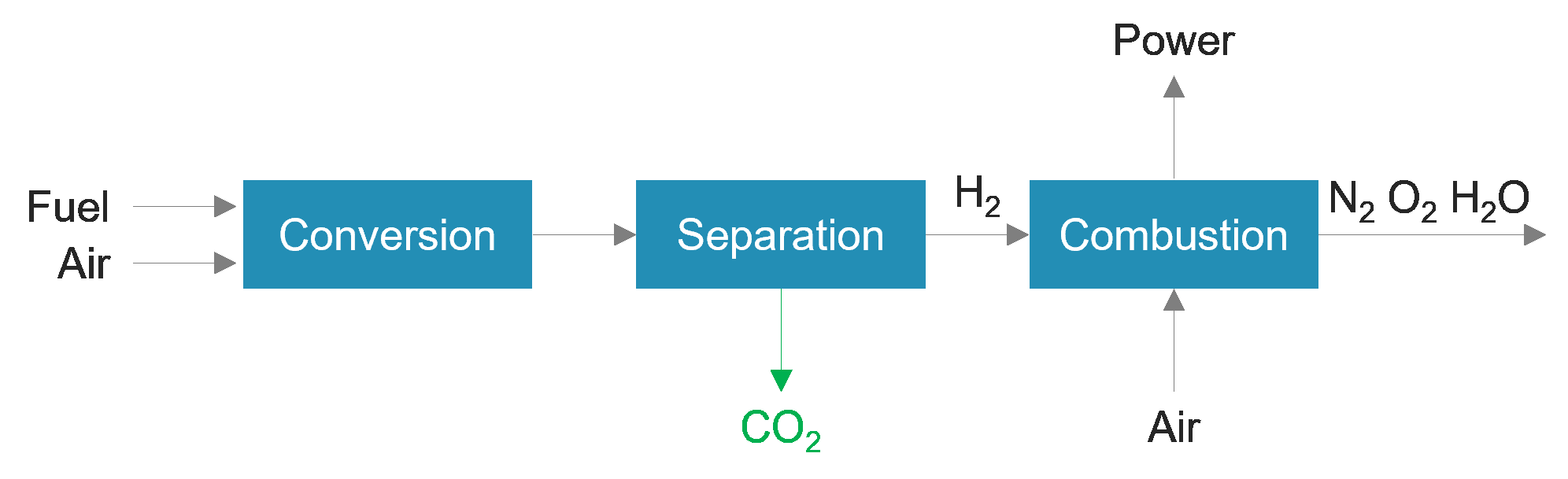
Following are few methods or techniques involved in pre-combustion carbon capture:
- Solvent absorption
- Adsorption
- Chemical looping gasification
Currently, pre-combustion carbon capture approach is applied to integrated coal gasification combined cycle (IGCC) power plants. Research and development are underway to commercialize the methods under this strategy.
Technology Comparison:
For various methods in both combustion strategies, the values for the following parameters shown in the table below vary with several factors such as working temperature, pressure, CO2 concentration in the flue gas, project or plant scale, environmental impacts, etc. Therefore, we have provided approximate information based on research and reviews conducted by several researchers.
Cost Analysis:
To install a carbon capture setup in any industry, economic feasibility is a high priority parameter. The cost analysis is conducted based on cost incurred in capturing 1 ton of CO2. Based on International Energy Agency (IEA) analysis, global cost of carbon capture per ton CO2 in various industries identified is shown below:
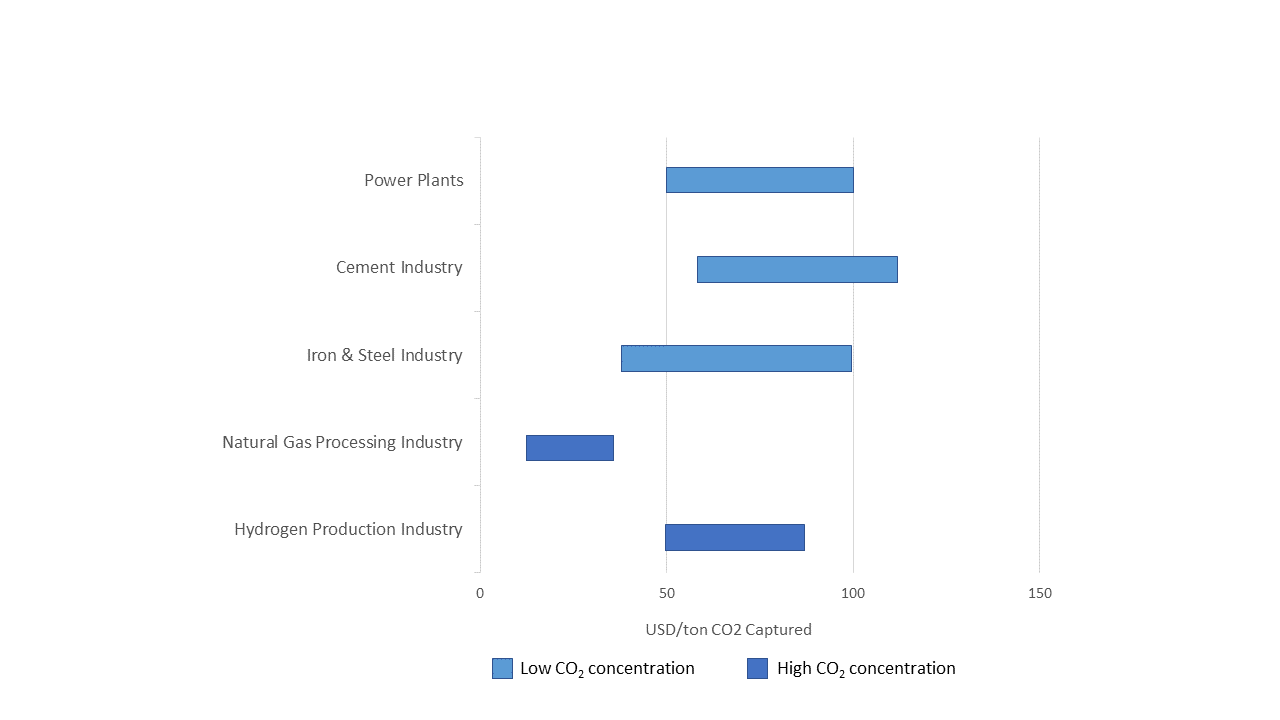
To achieve the lowest cost per ton of CO2 captured, most CO2 capture systems are designed to catch about 85–90% of the CO2 from the point source. Higher capture rates - reaching 100% - will be required in a net-zero energy system. According to recent analyses, this is technically and economically feasible.
Use Cases:
Post-Combustion Capture
- Absorption method – Steel industry: Tata Steel became the first steel business in India to use such a carbon-capture technology and achieve circular economy when a 5 ton per day (TPD) carbon capture unit was put into operation at its Jamshedpur (India) Works. Using an amine-based technique, this carbon-capture and utilization (CCU) facility takes CO2 right out of the blast furnace gas. The captured CO2 is then made available for reuse on-site. This project was conducted with the assistance of Carbon Clean, a world leader in low-cost CO2 capture technology.
- Membrane technology – Limestone factory: The Norwegian company Aqualung Carbon Capture won a contract to supply a membrane-based carbon capture and storage (CCS) system to a lime plant in Scandinavia owned by Nordkalk. According to the supplier, each Aqualung Carbon Capture unit can remove 25% of an average Nordkalk lime kiln’s CO2 emissions. The project will commence in the beginning of 2023.
- Cryogenic CO2 capture – Power plants & Cement plants: Sustainable Energy Solutions (SES) scaled this innovative technology with the largest being the skid system, which captures approximately 1 ton of CO2 per day. In field tests, this system captured 95–99% of CO2 with over 99% purity and initial concentrations ranging from 4% to 28% in the flue gas. SES now attempts to scale the system to merchant levels (10–80 tons of CO2 per day).
- Bio fixation – Power plant: Mannvit installed an algaennovation facility at Hellisheidi power plant where it uses CO2, hot water, and electricity from the plant, to sustainably turn waste to valuable product.
Pre-Combustion Capture
- Adsorption method – Hydrogen production: Xebec Adsorption Inc., a global provider of sustainable gas technologies, signed a contract to provide its proprietary pressure swing adsorption technology to support the deployment of Haffner Energy’s HYNOCA® solution. By thermolyzing biomass, HYNOCA®, a novel and cost-effective technology, can decarbonize and produce green carbon-negative hydrogen and renewable gases.
- Sorbent Enhanced Steam Reforming – Hydrogen production: A novel hydrogen generator technique developed by GTI Energy uses sorbent enhanced steam reforming (SER) to make hydrogen from natural gas while automatically capturing any CO2 produced in the process. Currently, two active demonstrations of this technology are taking place, one in the UK with assistance from the Department of Business, Energy & Industrial Strategy (BEIS) of the UK government and Cranfield University, and the other in Des Plaines, Illinois, US.
Takeaways:
Every industry has different requirements and operational methods; thus, the following factors must be evaluated before selecting the most viable CCUS technology.
- Retrofitting – As the industries needing this technology are well-established, techniques that can be retrofitted to existing industrial plants have more potential than other independently operating carbon-capture plants.
- Cost per unit capture – Establishing the capture method that makes capturing CO2 economically feasible.
- Carbon-capture rate – The method must be capable of capturing a significant amount of carbon from emissions.
- Purity – Carbon captured by any method must be of a high purity. The greater the impurities, the less efficient the carbon-based fuel that is produced during the utilization of captured carbon.
- CO2 concentration – CO2 concentration in flue gases also affects the efficiency of a given method.
Conclusion:
Numerous efforts are made to commercialize carbon-capture methods, but obstacles such as economic viability, emission of secondary pollutants, and high energy requirements continue to obstruct the path to net-zero emissions. Therefore, industries, particularly power, cement, and steel, must focus on methods or techniques feasible for their existing plants and reduce their carbon emissions as a high-priority metric, as opposed to directly implementing new technologies that are incompatible with their existing plants.
Stay tuned for the upcoming decarbonization articles in multiple industries such as cement, iron & steel, power generation, gas processing, and oil refineries.