Decoupling Supply Chains from China: A Complex Challenge
Published on 19 Jul, 2024
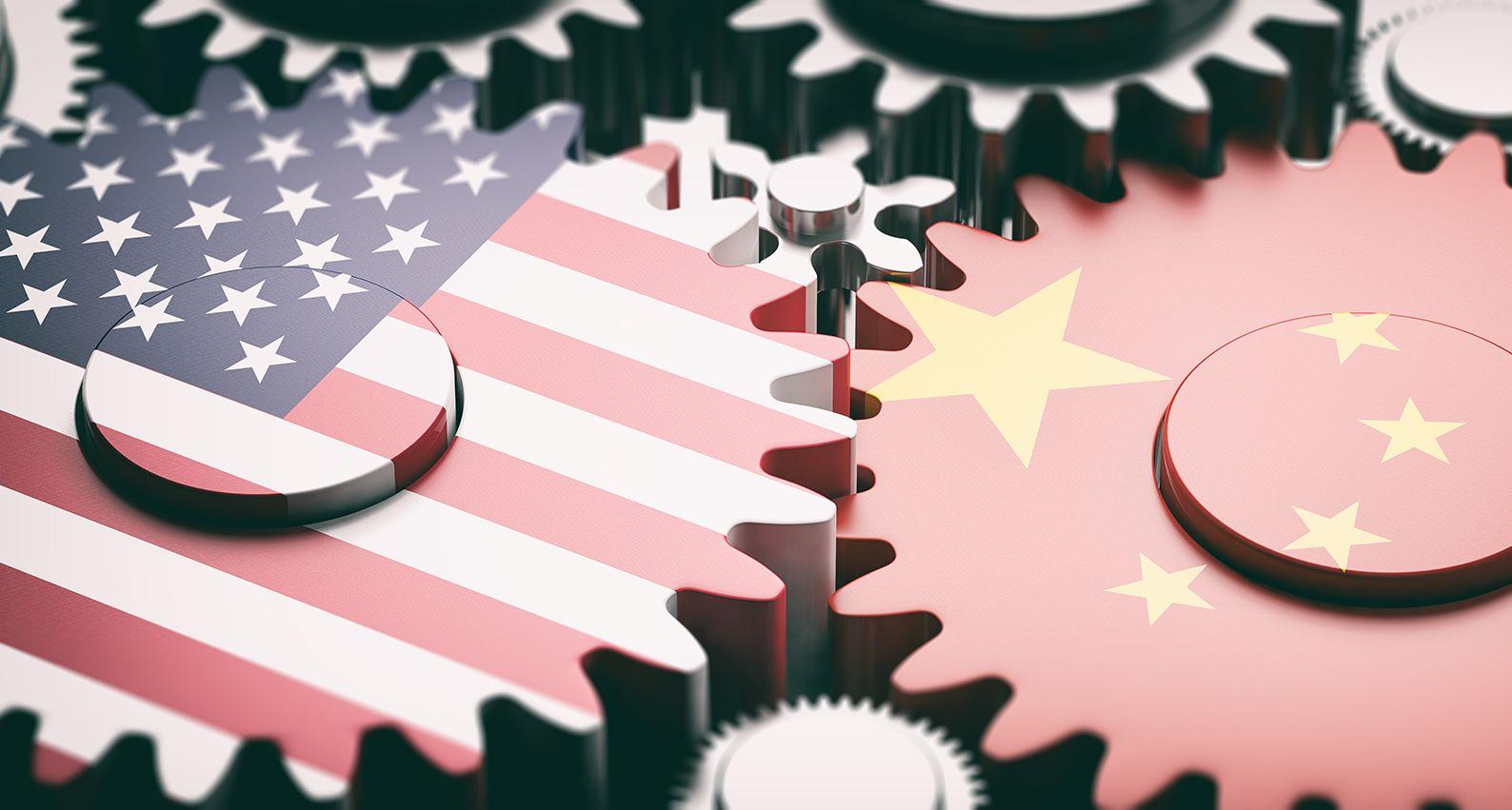
The US has a high dependence on Chinese imports, which complicates its supply chain decoupling strategies. While shifting final assembly to Southeast Asia and Mexico is relatively easy, intermediate stages like component production remain challenging due to China's established chemical industry and extensive production capacity. The automotive, electronics, and textile industries face significant disruptions when attempting to diversify their supply chains. The expertise, infrastructure, and cost-efficiency China offers are difficult to replicate elsewhere. Effective strategies to reduce dependence include government collaboration, tax incentives, and sustainable practices. A significant shift will be costly and best pursued in stable times, underscoring China’s pivotal role in global trade.
The US has an extremely high dependence on Chinese imports, and the notion of disconnecting from this economic giant is far more complex than it appears. While shifting some parts of the value chain is feasible, many elements pose significant challenges, primarily due to China's established chemical industry and overall production capacity.
The Easy Part: Shifting Final Assembly
Relocating final assembly processes is relatively straightforward. Many manufacturers have already begun moving electronics, automotive, and other assembly operations to Southeast Asia, focusing on countries like Thailand, Vietnam, and Taiwan. Mexico has also emerged as a significant player, now the largest source of US import volume.
The Difficult Middle Stages: Component Production
The real challenge in production often lies in the intermediate stages, where processes such as plastic/metal molding are essential for manufacturing product components. These stages rely on the complicated networks of global suppliers, the majority of which are present in China. Various sectors in the US heavily depend on Chinese components, including electronics, textiles, and industrial machinery. The intricacy of these supply chains makes it difficult to shift production without significant disruption.
China's Expertise and Infrastructure
China's extensive expertise in producing chemicals and intermediate goods is unmatched. It dominates the production of key chemicals like acetic acid and titanium dioxide, which are crucial for a range of industries from automotive to textiles. Accounting for over 40% of global chemical production, China has established itself as an indispensable player in the global supply chain. This dominance is supported by a well-developed infrastructure that other regions find challenging to replicate quickly. The sheer scale and efficiency of China's chemical production capabilities underline its critical role in global manufacturing and industrial processes.
Replication Challenges
Replicating China's capabilities in other regions is a significant hurdle. The expertise and infrastructure that China has built over decades cannot be easily or quickly duplicated elsewhere. Other regions face immense difficulty in matching the scale, cost-efficiency, and quality of production that China offers. This presents a substantial barrier for industries attempting to diversify their supply chains. The dependence on China's well-established systems and the complexity involved in developing similar capabilities elsewhere underscore the challenges faced by global manufacturers.
Industry-Specific Supply Chain Disruptions
US-based industries have faced significant supply chain disruptions amid their efforts to reduce dependence on China. The automotive industry, represented by companies like General Motors and Ford, experienced production delays and increased costs due to global semiconductor shortages and challenges while diversifying supply chains.
In the medical supplies industry, companies like Honeywell reported increased production costs and supply chain disruptions when sourcing products outside of China during the COVID-19 pandemic.
The electronics industry, with giants like Apple, Samsung, and HP, faced production delays, increased costs, and logistical challenges when shifting manufacturing to countries like Vietnam, Thailand, and India.
Similarly, the textile industry, including brands like H&M and Nike, encountered higher production costs, logistical challenges, and backlash when reducing reliance on Chinese cotton due to alleged human rights violations in Xinjiang.
Strategic and Sustainable Solutions
To effectively reduce dependence on China, a multifaceted approach is necessary, involving collaboration between governments and manufacturing companies. Key strategies include offering tax breaks and infrastructure support to incentivize relocation and implementing omni-shoring strategies to diversify sourcing locations, thereby mitigating geopolitical risks. In addition, sustainability considerations are crucial, as addressing the environmental impact of global trade ensures long-term acceptance and viability. By integrating sustainable practices, companies can meet regulatory requirements, enhance brand reputation, and contribute positively to the environment. This combined effort creates a more resilient and diversified supply chain network, reducing over-reliance on any single country and fostering a balanced global trade system.
The Big Picture: China's Role in Global Trade
Over 2023-24, China accounted for approximately 15% of global merchandise exports and about 14% of global imports, solidifying its position as a central hub in the world's supply chains. The country's chemical industry alone constitutes over 40% of global chemical production, underscoring its critical role in manufacturing and industrial processes.
A significant shift of supply chains away from China will be an expensive endeavor, best undertaken during times of relative peace and stability rather than crises. The interconnected nature of modern manufacturing implies that while the initial phases of relocation are manageable, the deeper, more value-added stages require substantial investment and coordination. Addressing these challenges proactively will ensure resilience and sustainability in global trade.