3D Nanoprinting: The Next Frontier in Precision Manufacturing
Published on 10 Oct, 2024
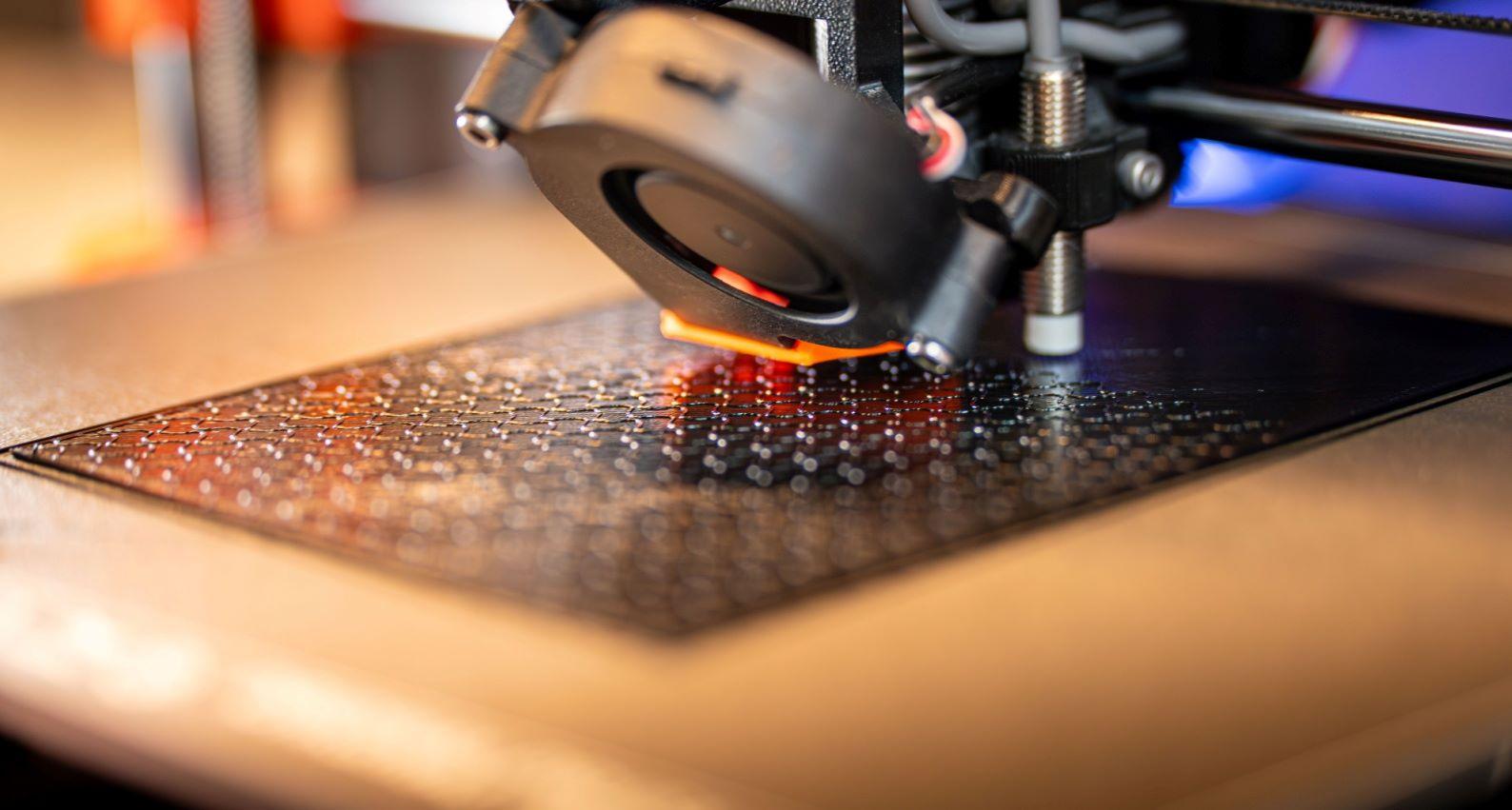
3D printing has rapidly transformed traditional manufacturing, shifting from producing basic plastic components to creating highly intricate structures in metals and other materials. The most recent and exciting advancement in this field is nano 3D printing, which pushes the boundaries of precision and customization at the nanoscale. This breakthrough technology is opening possibilities for a wide array of industries, including healthcare, electronics, and aerospace, by enabling the production of complex nanostructures that were previously unattainable.
While traditional methods such as micro-stereolithography (µSLA) and two-photon polymerization (TPP) have been central to the creation of nanoscale structures, recent innovations in nano-printing have introduced more sophisticated techniques across various research institutions. These advancements are now driving significant progress in areas where ultra-precision and customization are critical. Let's delve into some of these cutting-edge methods that are redefining nano 3D printing capabilities.
- Laser-Based Method - Developed by Wuhan University, China, this method uses ultrafast lasers to create nanoscale metal structures by decomposing metal carbonyl solutions such as cobalt and tungsten. These layers are then processed to eliminate impurities, producing precise 3D metal components. Laser technique enables the creation of highly intricate designs, especially valuable for microelectronics and precision optics.
- Electron Beam-Based Methods - At Henan University, electron beams in a vacuum environment are employed to assemble 3D structures by focusing on atomic diffusion. The technique is ideal for applications that require extreme precision, such as superconducting materials.
Zhejiang University has further innovated with ice-assisted electron-beam lithography (iEBL), which replaces traditional photoresists with ice. This reduces fabrication time, making it especially effective for producing nanoscale components in sensors. Other advances at institutions such as Graz University, Oak Ridge National Laboratory, and University of Tennessee concentrate on focused electron beam induced deposition (FEBID), where electron beams decompose precursor materials to create nanowires and other conductive elements for electronics and medical devices. - Electric Field-Based Method - Researchers at Shanghai Technology University have developed a 3D printing method that uses electric fields to precisely arrange charged species dispersed in a fluid at the nanoscale, enabling the creation of intricate nanostructures. This method stands out due to its ability to operate at room temperature and use a variety of materials, making it highly versatile across numerous industries.
- Microfluidic/Aerosol-Based Methods - At Seoul National University, a microfluidic-coupled atomic force microscope (FluidFM) and aerosol-based techniques enable rapid crosslinking of polymers, allowing for highly precise nanostructures. This method is particularly useful in biotechnology and photonic systems. Similarly, Korea Institute of Machinery & Materials has introduced multi-syringe systems to enable molecular-level precision printing.
- Hologram-Based Method - Chinese University of Hong Kong has taken nano 3D printing further by employing holography to enhance two-photon lithography, enabling rapid printing of complex nanostructures at a remarkable resolution of 90 nanometers.
- Electrochemical Method - Research from University of Oldenburg, ETH Zurich, and Nanyang Technological University has pushed the boundaries of precision with electrochemical techniques that allow for the creation of 3D copper structures as small as 25 nanometers, particularly promising for energy storage and microelectronics applications.
- Combination of Different Methods - Jinan University has demonstrated the benefits of combining laser powder bed fusion (LPBF) with laser-induction hybrid cladding (LIHC) to create composite metal structures. This hybrid approach allows for greater material flexibility and is ideal for industries that require high-strength components with enhanced material properties, such as aerospace and automotive.
The potential applications of nano 3D printing are vast, especially in industries that demand high precision, scalability, and innovative material use:
Healthcare: Nano 3D printing has become integral to advancements in biomedicine, including drug delivery systems, micro-needles, and implantable devices. For instance, Fertilis Pty Ltd used this technology to develop microfluidic devices for in vitro fertilization (IVF), reducing cycle times by 30-40% by accurately controlling embryonic environments, improving IVF success rates.
Electronics: The electronics industry greatly benefits from the miniaturization enabled by nanoprinting. Stanford University has developed Archimedean truncated tetrahedrons (ATTs), which are shapeshifting nanoparticles capable of optimizing solar panels, creating hydrophobic films, and enhancing memory systems for advanced computing. Additionally, KTH Royal Institute of Technology in Stockholm pioneered nanoprinted glass sensors on optical fiber tips, designed for highly resilient remote sensors used in environmental monitoring, healthcare, and quantum communication systems. Nano 3D printing's ability to produce intricate nanostructures and custom optical components has revolutionized sensor technology and photonics.
Energy: Nano 3D printing is also making significant strides in energy applications. Korea Electrotechnology Research Institute developed techniques to 3D print pure graphene nanostructures, which are key to improving the efficiency of solar cells and sensors.
Architecture: Innovative designs in architecture and decoration have emerged through nano 3D printing. ETH Zurich replicated the vibrant colors of butterfly wings by printing nanoscale patterns, which offer eco-friendly and durable alternatives to traditional pigments. This has potential applications in high-resolution displays, security features, and color filters.
Nano 3D printing represents a significant leap forward in precision manufacturing, allowing for the creation of complex and customizable structures at previously unattainable scales. Among the many methods explored, electron beam-based techniques stand out for their versatility and application in both electronic and medical devices, while laser-based methods are rapidly advancing the manufacturing of high-quality metal components. This technology has already made considerable inroads in healthcare, electronics, energy, and architecture, but its potential is far from exhausted.
Looking ahead, nano 3D printing is expected to play a pivotal role in fields such as tissue engineering, where precise control over biological materials could revolutionize regenerative medicine. The combination of these advanced methods, along with continuous innovation, ensures that nano 3D printing will remain at the forefront of technological advancements across a wide range of industries.